Our Motor Rewind Process
- Initial Inspection: Assessing the motor’s condition to identify potential issues and determine the scope of repairs.
- Repair Requirements: Evaluating the extent of damage and outlining necessary repairs to restore optimal functionality.
- Insulation Materials: Utilizing premium-quality insulation materials to enhance durability and longevity.
- Rewinding: Expertly removing old windings and replacing them with new ones to ensure reliable performance.
- Precision Work: Ensuring meticulous winding to prevent vibration and maintain operational stability.
- Quality Assurance: Conducting thorough testing to validate performance and reliability, ensuring customer satisfaction.
- Minimizing Downtime: Maintaining a well-stocked inventory of replacement parts for swift access and minimal disruption.
- Final Inspection: Performing a comprehensive assessment to confirm adherence to quality standards before returning the motor to the customer.
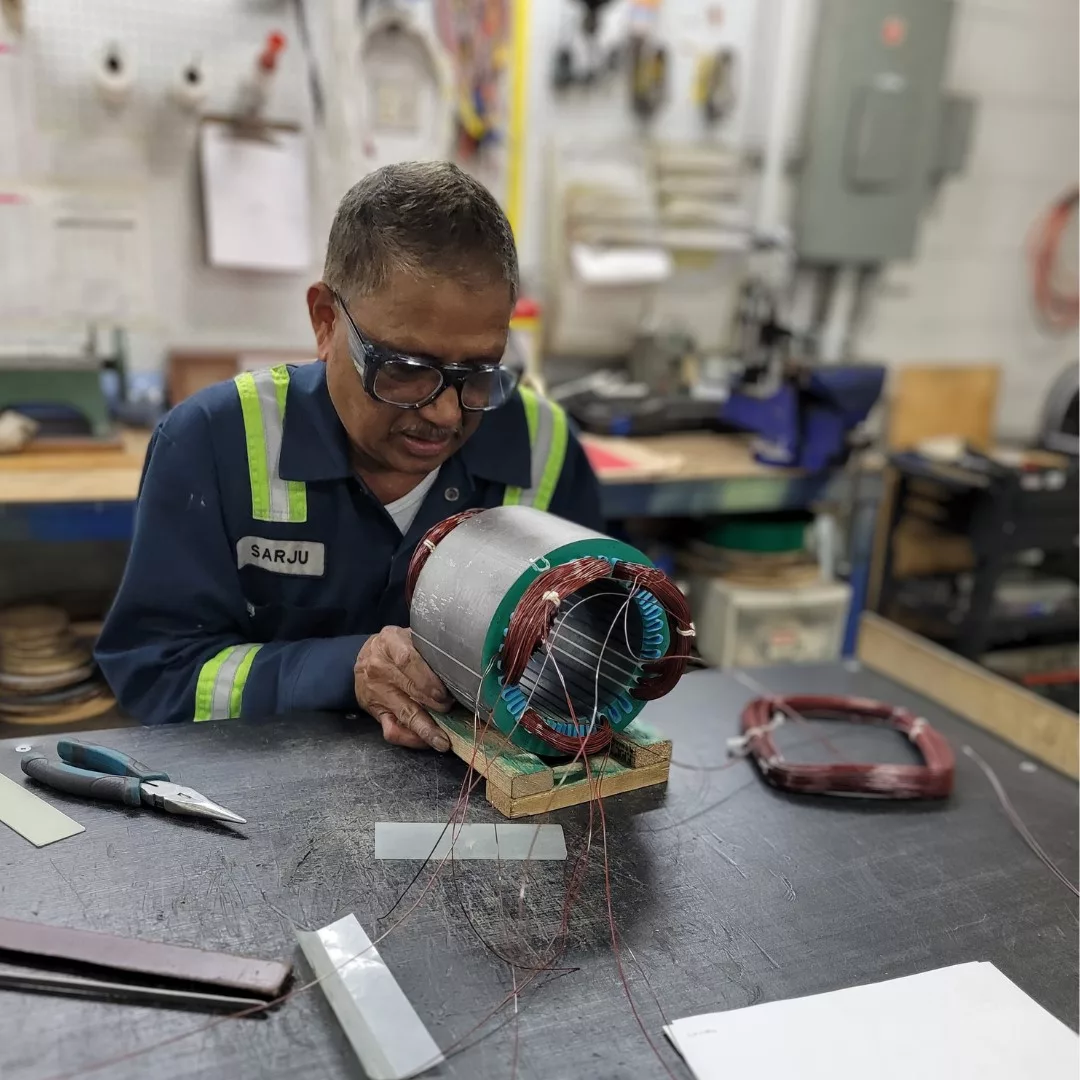
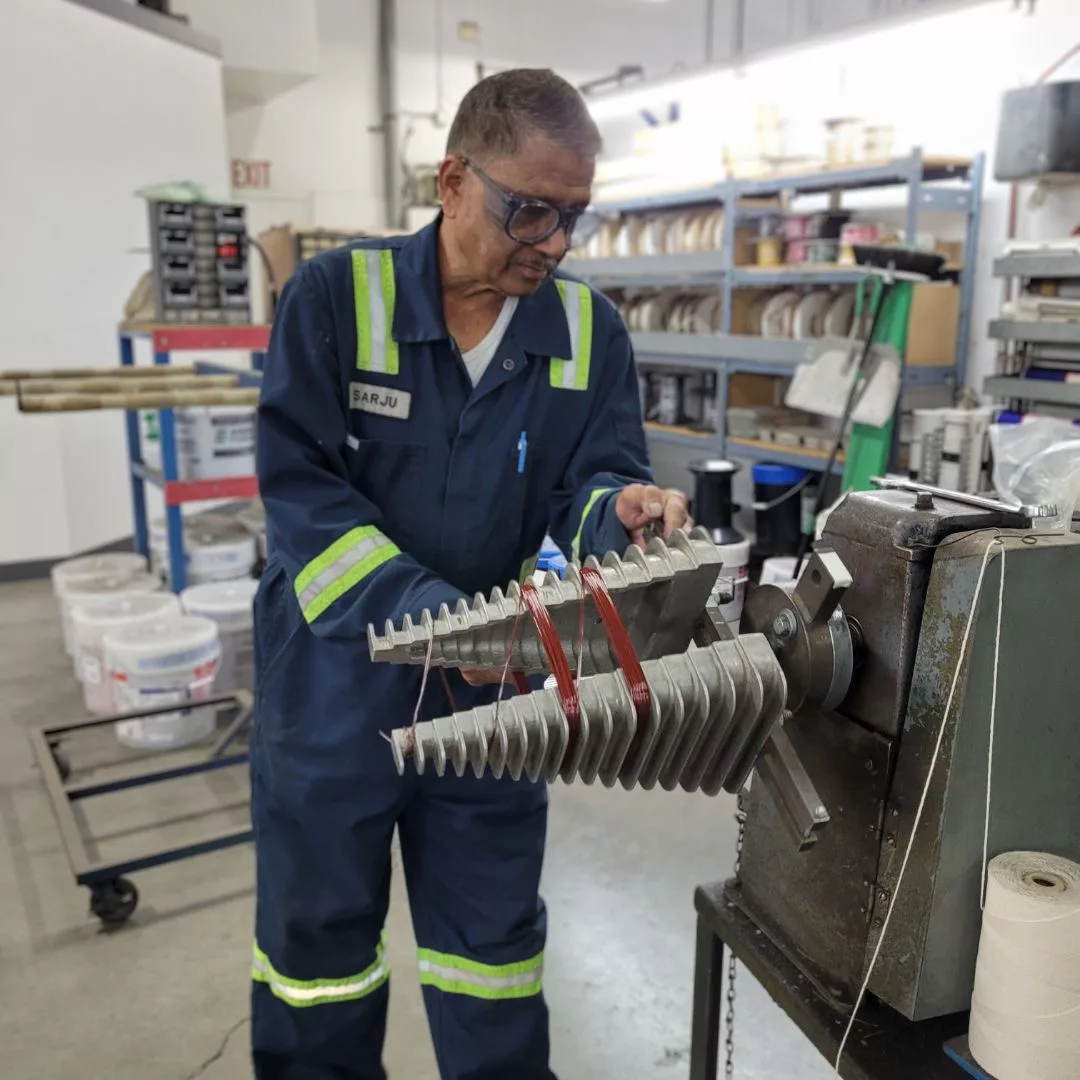
Your Motor May Need a Rewind if…
1. Signs of Excess Wear or Deterioration
Your motor may need a rewind if you notice signs of deterioration, like burns, broken parts, or contamination from moisture or rust. Electric motors typically have a long lifespan, but wear and tear can still take its toll over time.
Rewinding can be a more affordable alternative to buying a new motor, as it can cost up to 40% less. This is especially true if you own larger motors, which can be costly to replace. During an inspection, a technician may suggest rewinding if the laminations inside the motor remain undamaged.
Rewinding your motor can be a great option if you want to save money or don’t have the resources to buy a new one. It’s also the way to go if you have larger motors that can be pricey to replace. Plus, if the laminations within the motor aren’t damaged, rewinding is an ideal choice.
However, you should be aware of the signs that your motor needs rewinding. These include burns, broken parts, and contamination from moisture or rust. Electric motors tend to be long-lasting, but they’re still susceptible to gradual wear and tear.
Rewinding your motor is more cost-effective than replacing it, as it can cost up to 40% less. Plus, it’s a great way to restore your motor if the laminations remain in good condition. Before rewinding, make sure to look out for any signs of deterioration, such as burns, broken parts, or contamination.
2. Poor Winding resistance
If an electric motor isn’t performing as it should, a motor shop or electrician would typically measure its winding resistance. This test helps detect if shorted coils are causing issues. The recommended winding resistance levels are usually stated on the motor’s nameplate or in the manufacturer’s documentation. If the numbers don’t match up to the measurements taken, a rewind could be necessary.
Replacing the motor is an option, however, rewinding would be more cost-effective and environmentally friendly. Core materials are reused, resulting in a much lower carbon footprint than creating a new motor. Plus, it’s a great way to recycle and make use of what’s already available.
3. Problems with insulation resistance
Electric motors are vulnerable to winding faults, which can be a huge problem. Heat has a serious impact on the components inside a motor, and when the insulation resistance is low, it can lead to reduced lubrication, damaged parts, and other issues. That’s why it’s so important to be aware of how insulation resistance can affect an electric motor. Taking the necessary steps to ensure the insulation resistance is high enough can save you a lot of trouble.
Insulation resistance can drop over time, due to contamination, vibration, and power surges. Rewinding an electric motor is a great way to improve the insulation resistance and the efficiency of your motor.
Taking your motor to an experienced motor shop for the rewinding process is recommended. With the use of advanced techniques, along with top-notch resins and insulating tapes, the efficiency of an electric motor can be significantly improved. Finding the right team with the proper experience is the key to a successful and cost-efficient motor rewind.
These questions will help you make the right decision regarding your motor. Consider these points carefully and make a wise decision – one that will save you money in the long run.
What does it cost for an electric motor rewind?
This will vary depending on the size and HP of the motor. Having your motor rewound can be anywhere from 40% to 70% of the price of a brand-new motor. In addition to saving money, choosing to rewind your motor can also help the environment. The rewinding process has a very minimal environmental impact when compared to the carbon costs of creating a brand-new motor and disposing of the old motor.