Electric motors have certainly made significant progress in design and performance over the past 150 years. However, their primary function remains the same: converting electrical energy into mechanical movement.
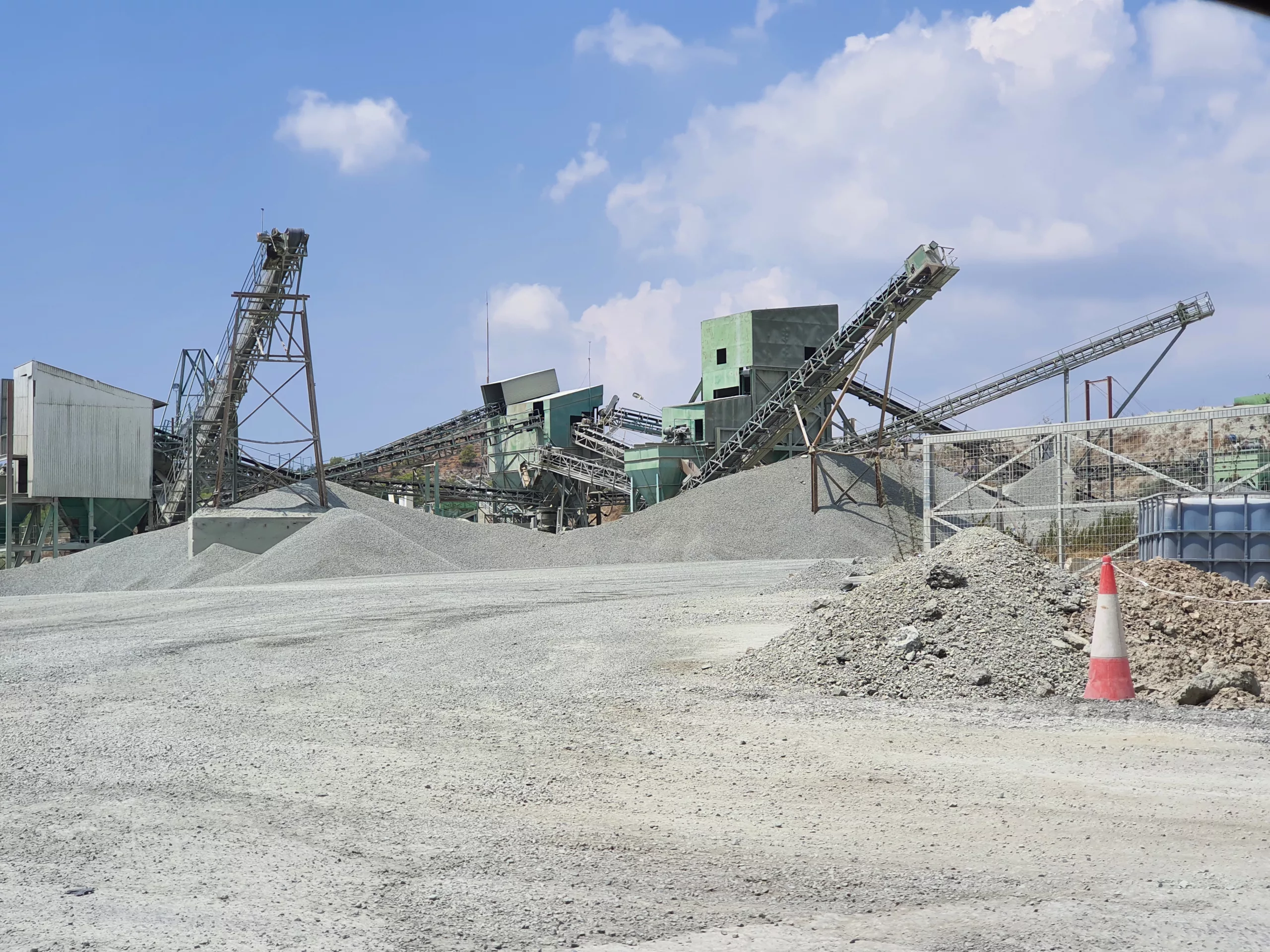
These motors are integral to almost every industry – many of which some may not even think of. For instance, electric motors power a wide range of equipment in the aggregate industry, such as crushers and conveyors. These machines are essential for processing materials like crushed rock, sand, and gravel, which are the building blocks of infrastructure and construction projects.
Food production companies also heavily depend on electric motors. Motors drive many components of food production lines, including conveyors, mixers, grinders, packaging machinery, and cooling systems. Without them, the efficiency and quality of food processing would be greatly compromised.
Hospitals and large post-secondary campuses heavily rely on electric motors to move air and water throughout their buildings. These motors are essential for maintaining a comfortable and safe environment for patients, students, and staff.
But, as with any mechanical device, an electric motor can suffer from a range of issues, including damaged interior components all the way to harm caused by exposure to contamination. In reality, there are a number of reasons that can cause electric motor malfunctions. Their failures can lead to costly downtime and production interruptions.
Addressing these issues and ensuring the smooth operation of electric motors falls into the capable hands of maintenance professionals. Their work is essential, but it can be a complex and demanding task. Regular maintenance and timely repairs are necessary to prevent costly downtime and keep machinery operating at its best.
In this article, we will explore the repercussions of downtime and production interruptions, the most common problems with electric motors that lead to downtime, and the different solutions Universal Rewind offers to diverse industries across Western Canada.
Understanding the Impact of Unplanned Downtime
Unexpected equipment breakdowns or maintenance tasks that lead to machine shutdowns can cause significant production downtime and financial losses, including expenses such as lost revenue, missed order deadlines, increased labor costs during recovery, and potential penalties for delayed shipments.
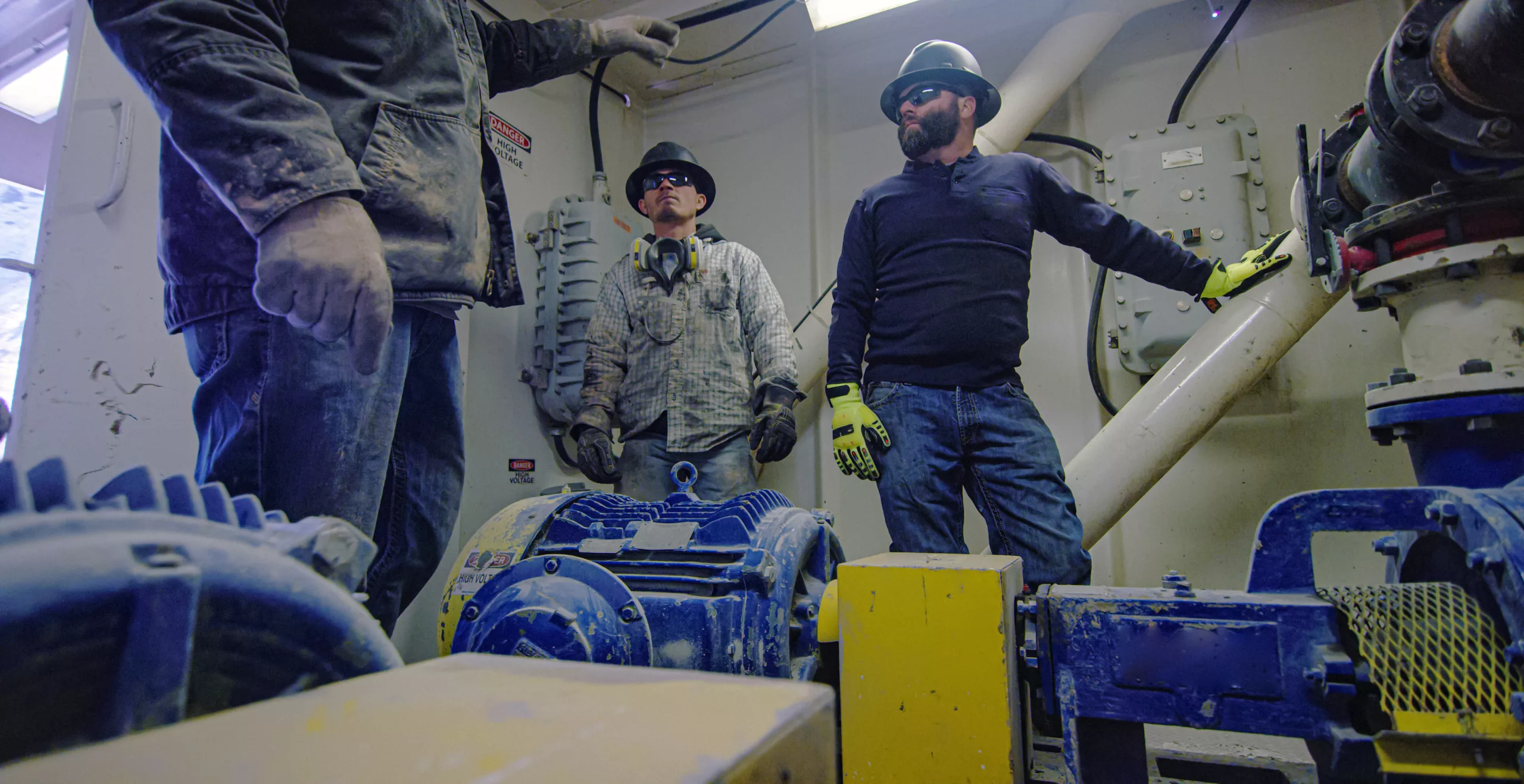
For some perspective, Fortune Global 500 (FG500) manufacturing and industrial firms are estimated to lose about 3.3 million hours each year due to unplanned downtime. The financial impact of this downtime on these organizations is approximately $864 billion, equivalent to eight percent of their annual revenues.
This unplanned downtime can often be attributed to numerous different factors, including ageing equipment. Many production facilities use older machinery that may require more frequent and specialized maintenance, a challenge encountered by various industries worldwide.
Across the border in the United States, for example, the average factory is more than 25 years old, with the equipment inside often exceeding nine years of age. Sourcing replacement parts for these older machines can also be challenging. While reactive maintenance, where repairs are done only after equipment fails, can be costly and disruptive.
Maintenance professionals can create preventive maintenance programs, which can certainly help but require careful planning and execution, adding to their workloads.
Most Common Malfunctions in Electric Motors
Electric motors can run into all sorts of issues that maintenance professionals need to be aware of if they are to fix them right. At Universal Rewind, we’ve teamed up with companies in many different industries, like Aggregate, Mining, Food and processing, Electrical Contractors, Oil & Gas, and Manufacturing. We’re here to help you grasp the everyday problems that electric motors can have, so we’ve put together a list for you.
1. Overheating
Electric motors naturally produce heat during operation. While some heat is normal, excessive overheating can lead to damage and the deterioration of internal components. Even a slight increase in temperature can wear down vital parts, such as bearings or the insulation in the windings. The key to reducing your risk of unexpected motor failure is regularly checking for operational overloads. is essential to prevent unexpected motor failures.
It is also important to ensure you source the appropriate motor in the first place. There are a number of enclosure types, from Totally Enclosed Fan Cooled to Open Air, each being more or less appropriate for different applications.
2. Power Inconsistency
All electric devices require a specific amount of power to function correctly. If a device accumulates more energy than it can handle, it may experience a power surge, resulting in malfunctions. To prevent this, many organizations install variable speed drives to mitigate the impact of unexpected power imbalances. If your electric motor lacks such protection, consulting an expert for suitable solutions is advisable. When using VFD we recommend installing shaft grounding rings (or having your local shop/Universal Rewind install them for you) to prevent bearing damage.
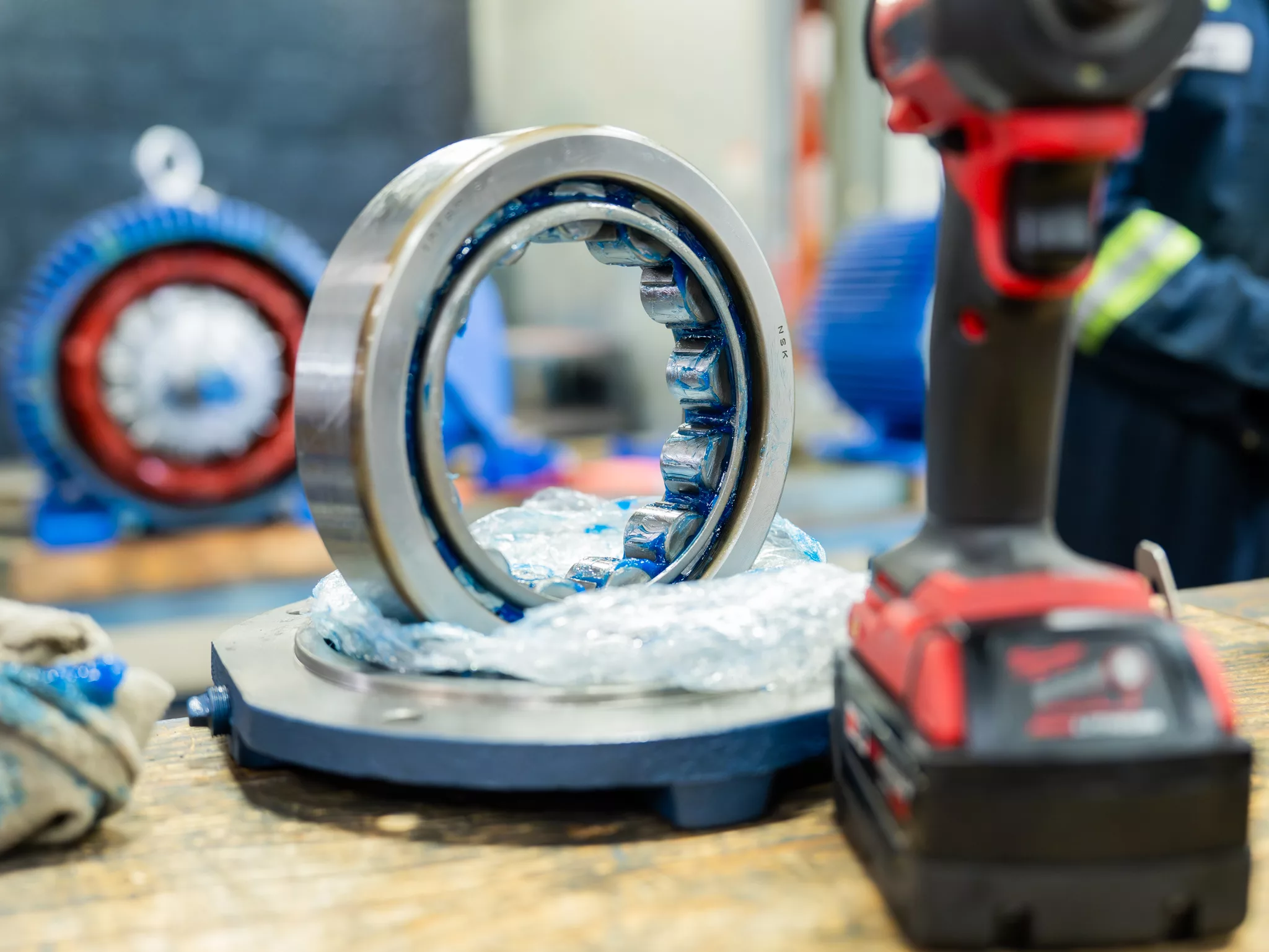
3. Bearing Wear and Failure
Bearing issues account for up to 13% of all electric motor failures. Despite their small size, bearing failures can lead to problems like overheating, insufficient lubrication, and increased friction. Common causes of bearing problems include misalignment, excessive loads, and improper fits. Identifying early signs of bearing damage, such as excessive motor vibration, is a valuable method to prevent significant performance issues. As noted in #2, we recommend using shaft grounding rings wherever you are using vfds.
4. Moisture and Humidity Exposure
Electric machinery and moisture are a problematic mix. Preventing moisture and humidity in a work environment can be challenging. Water exposure can damage the motor’s insulation, reducing its overall lifespan. Storing the motor in a warm and dry location is crucial. Additionally, installing humidity-monitoring devices can help maintain low humidity levels, reducing the risk of long-term damage and corrosion caused by moisture.
As we always recommend, selecting the appropriate motor for a given application is crucial. If the motor operates in an environment where moisture is a key concern, choosing a TEFC (Totally Enclosed Fan-Cooled) or Washdown (if needing a motor that is suitable for low to high-pressure washing) enclosure motor is highly advisable. This choice ensures that unwelcome contaminants are effectively prevented from infiltrating the motor, increasing its longevity and reliability.
5. Harmonic Distortion
Harmonics, referring to unwanted high-frequency electric voltages and currents, can disrupt an electrical system’s performance. The excess energy from harmonics is distributed to the motor’s windings and bearings, resulting in internal energy losses. Over time, harmonic distortion can reduce the insulation’s effectiveness, making the motor more susceptible to performance issues. Reducing harmonic distortion can be achieved by installing a variable frequency drive or using filters to minimize harm from harmonic distortion.
6. Contamination and Corrosion
Contaminants, in the form of dirt, dust, and abrasive substances, are prevalent and can enter a motor’s internal components, causing corrosion and wear over time. Preventing contamination and corrosion involves:
- Implementing safe work practices.
- Using appropriate lubricants within the machine.
- Maintaining clean workspaces.
- Positioning the motor away from machines that might introduce air contamination.
- Ensure you have the proper enclosure for your application. (Washdown Motors)
To sum up, many elements and contributing factors can cause electric motors to malfunction, halting your operations. If you want to keep your machines humming along smoothly for as long as possible, it’s a sensible idea to go for ongoing preventative maintenance, which is where our team crew at Universal Rewind can help.
Expert Electric Motor Repair Services by Universal Rewind
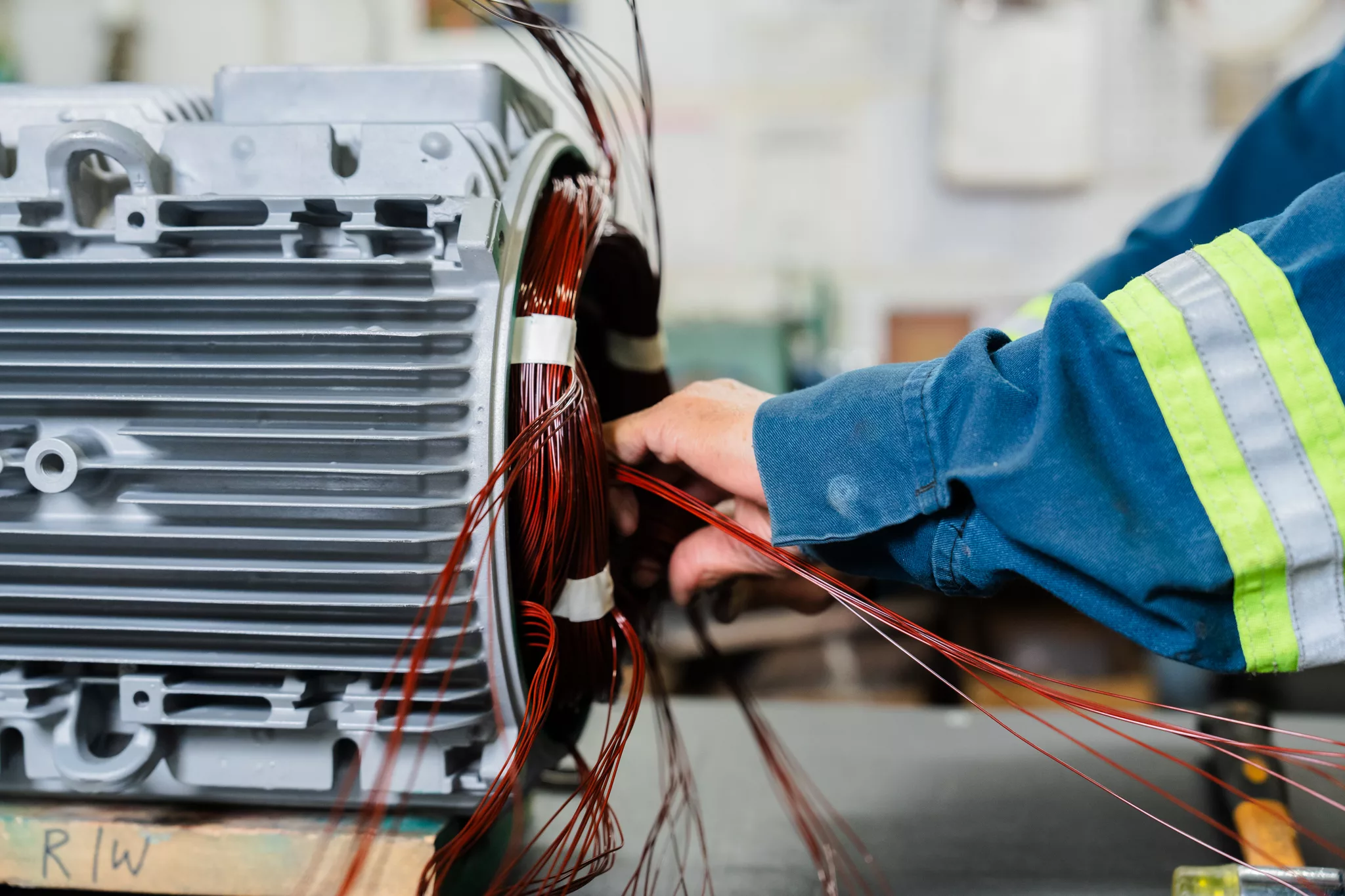
At Universal Rewind, our focus lies on Electric Motors and the Repair Services associated with motors– that’s our specialty. We cover everything from motor rewinding and routine maintenance to repairs and if needed, motor upgrades. Additionally, we extend our expertise to certain pumps and generators.
We’re incredibly proud of our experienced and skilled technicians. They are the backbone of our operation, ensuring we provide excellent service to all our clients. They bring expertise and dedication to the table, making sure your equipment runs smoothly.
This means maintenance professionals across a number of industries can rely on our services to keep their machinery running efficiently and minimize downtime. Our team of experts is ready to tackle any electric motor-related challenge, providing tailored solutions to ensure your operations remain in top gear.
Find out how our wide range of Industrial Electric Motors, Motor Controls, Gear Reducers/Gearmotors, and Repair Services benefit you and help drive your operations forward.
Leave a Reply